OUTLINE CHAIR - MOLTENI&C
DESIGN BY ARIK LEVY
Molteni turned to Viola Srl for the development of the metallic structures for a new innovative chair.

REQUEST
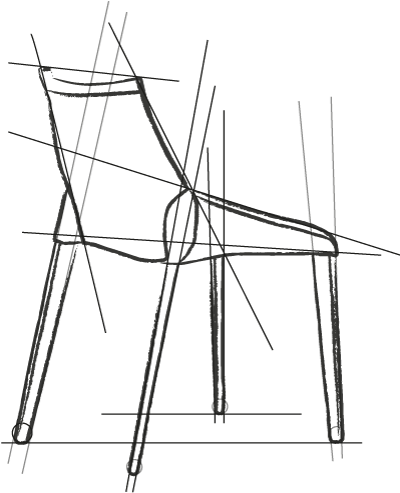
To create one or more metallic support frames for an innovative chair with the following characteristics:
• available for different chair models: fully upholstered and with high-end finishes;
• light but extremely resistant;
• easy and fast to assemble due to the high production volume → 5000chairs/years.
FIRST HYPOTHESIS
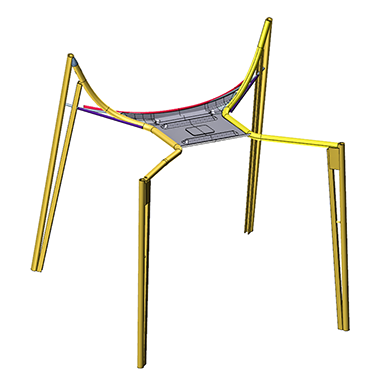
HYPOTESIS 1
Create 3 frames,one for each type of finish:
type.01 fully upholterstered
type.02 leather seats and wooden legs
type.03 leather seats and chromed legs.
ANALYSIS
pros:
- Less variables to consider;
- Faster development.
cons:
- Difficulty in predicting the volumes of finishes;
- Logistic and supply problems;
- Triple number of production equipments.
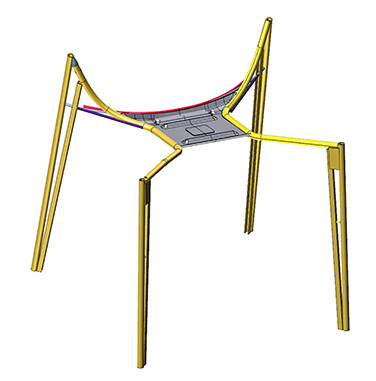
HYPOTESIS 2
Create 1 universal support frame for the seat base and legs and leg carters (metal leg covers) in aluminium customizable in the following finishes:
finish.01 light chrome
finish.02 dark chrome
finish.03 wooden veneers
ANALYSIS
pros:
- Only one frame for all versions;
- Only one set of production equipment
- Fast processing of customer orders with the possibility of a quick global delivery
cons:
- High complexity of engineering and design that include development of specific equipment and new machinery add-ons dedicated exclusively to this product in our factory.
DEVELOPMENT OF THE CHOSEN HYPOTHESIS
With the goal of dispatching orders quickly, the client opts to proceed with the idea of one universal support frame and alluminium carters with custom finishes.
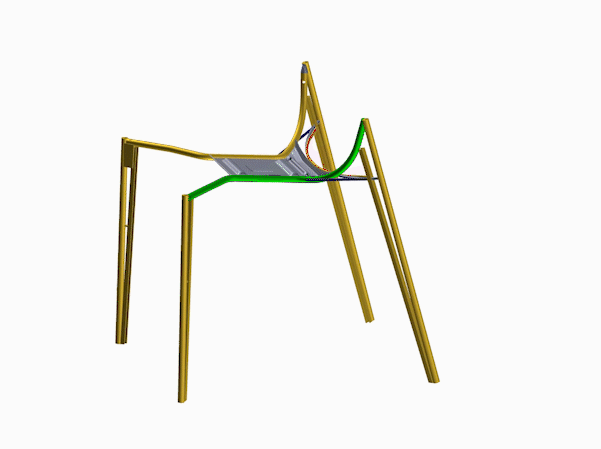
FIRST 3D MODEL
When designing we've considered the following production specifications:
• Utilization of thinner tubular steel with a reticular structure for lightness and higher stability;
• Sliding carters (leg cover) placed over the frame structure - seat base and legs - which are then fixed by rubber feet tips;
• Chair hooked through screws on the frame that do not remain visible when the chair is fully assembled;
• Seat frame made of carbon steel sheets which are reverse deep drawn and then profiled.
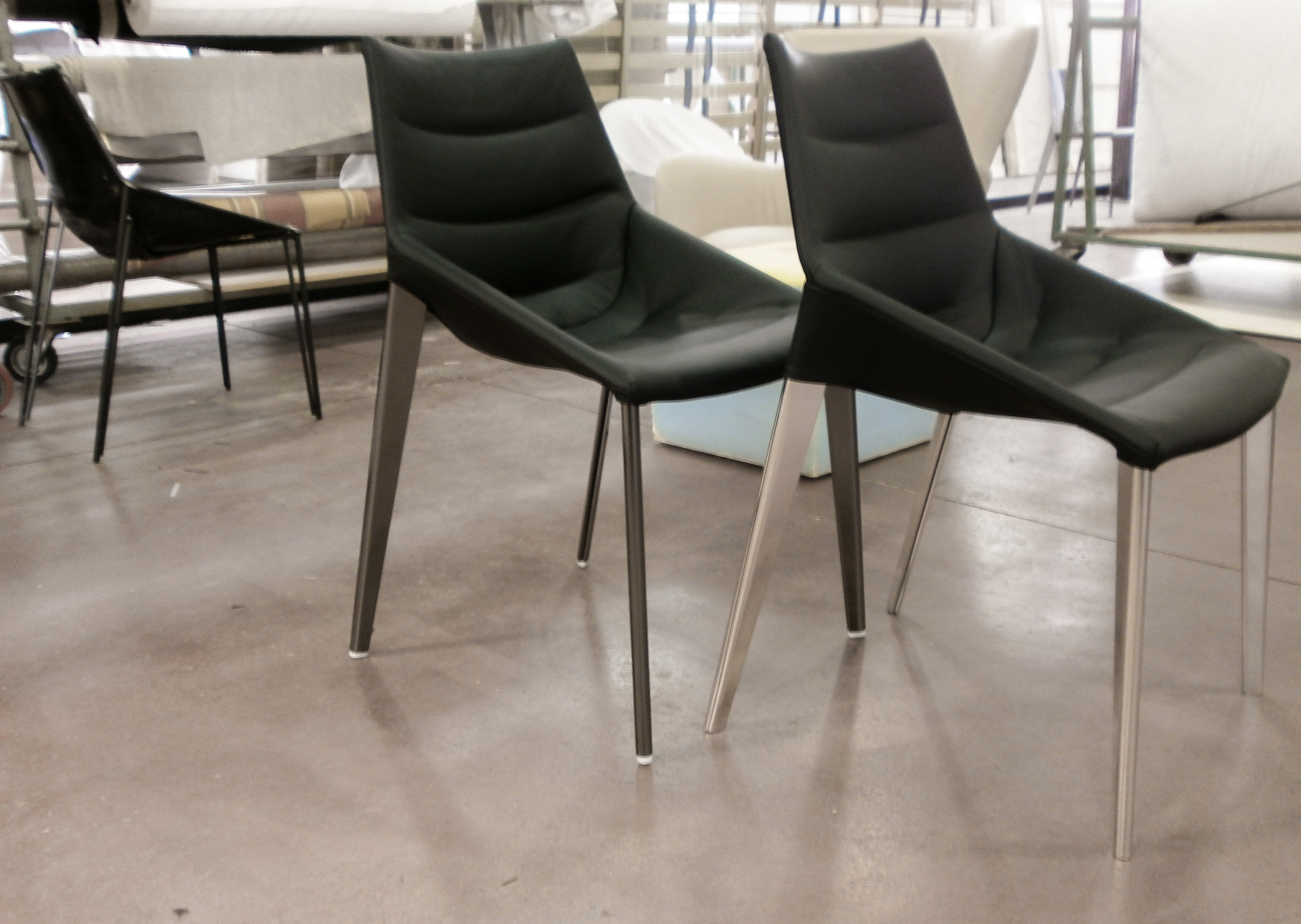
MOCK-UP
A first mock-up of the frame made with square steel tubes is presented to the client along with the first examples of carters, all without the use of custom macchinery in this fase.
The mock-ups are presented to the client and during the meeting a few necessary changes are in order:
• tubular steel of the support frame switched from square to circular;
• support frame to be finished by standard with matte black powder coating;
• Molteni's logo is to be marked on the central sheet of the frame;

MEETING WITH OTHER SUPPLIERS
After meeting with the manufacturers of the other chair components, such as padding,upholstery and glass fiber seat molds, a few improvements are made:
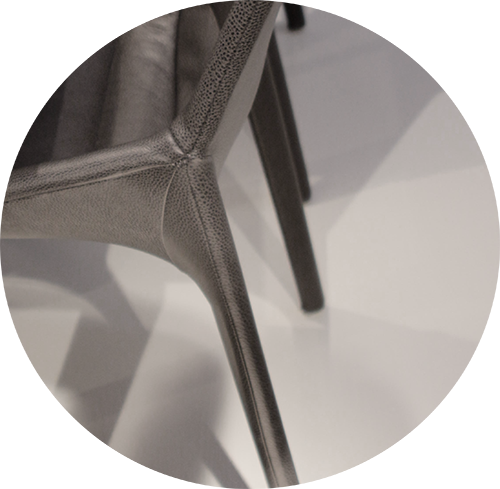
• For a faster assembly of the chair the insertion angle of the latching screws is modified
• Tensioners are placed on the frame to better maintain the shape of the fabric or leather upholstery
• Adjustment to the frame geometry for an improved aesthetic of leather uplholstery
PROTOTYPES
After a 4 month development process, by the end o March, 12 chair frame prototypes are delivered, in time to be assembled and exhibited at the following Salone del Mobile, which takes place once a year by the end of April 2012 in Milan, Italy.
THE PRODUCTION
From the first showcase at Salone del Mobile until the dispatch of the first order, 3 months went by, which where necessary for the production and the creation of the following equipment:
1. Welding fixtures in a dedicated robot zone for the leg components of the frame;
2. Marking stamps of the Molteni logo for the seat base;
3. Custom bending and metalization equipment for the production of the aluminum finish variant of the leg components;
4. Assembly template of the frame;
5. Coating fixtures for the frame;
6. Design of packaging for the transportation of the frame and leg components.
DELIVERY
July 2012 marks the begining of the first deliveries of the produced metal components. It was the beggining of a long collaboration between Viola and Molteni that is still going strong.
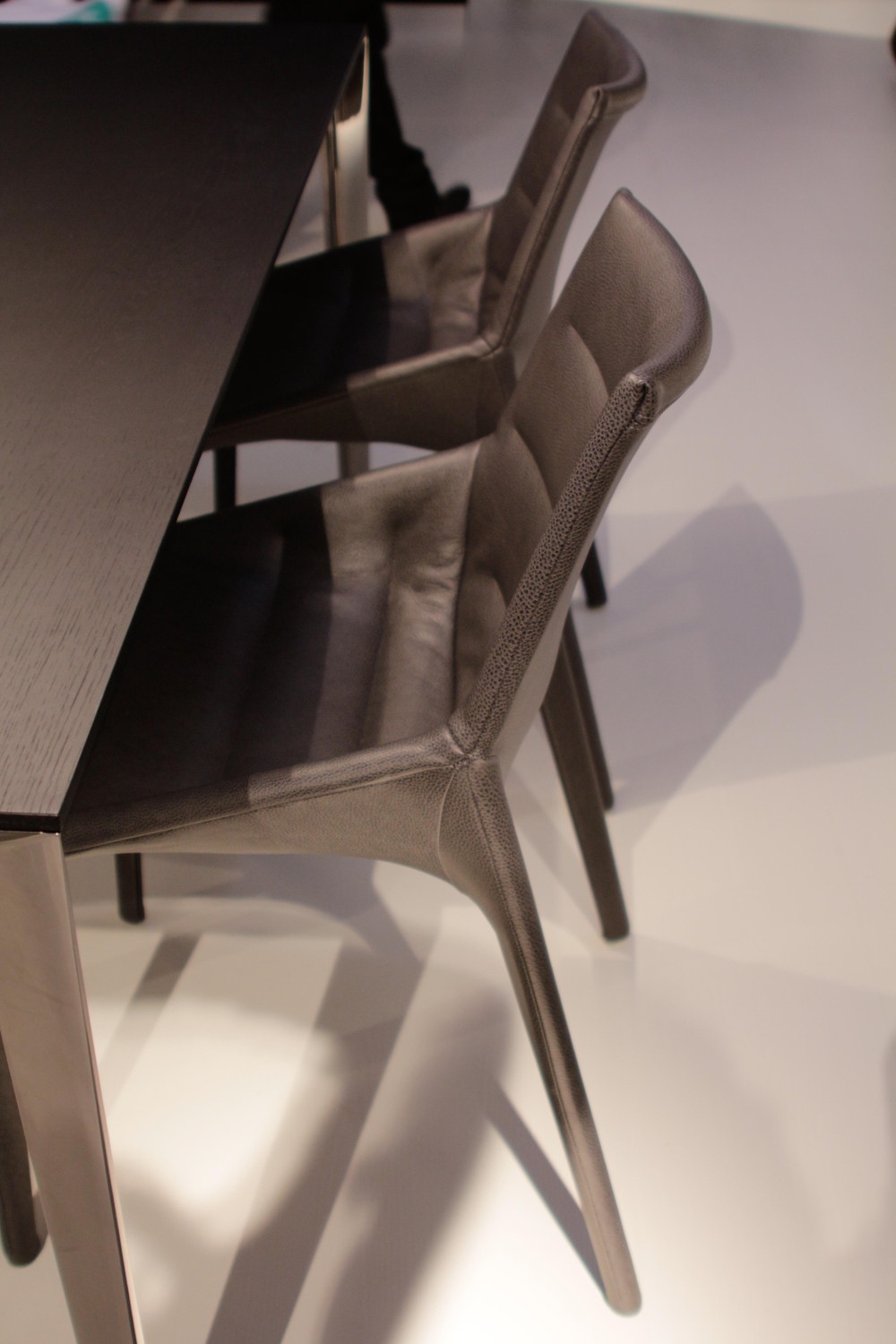
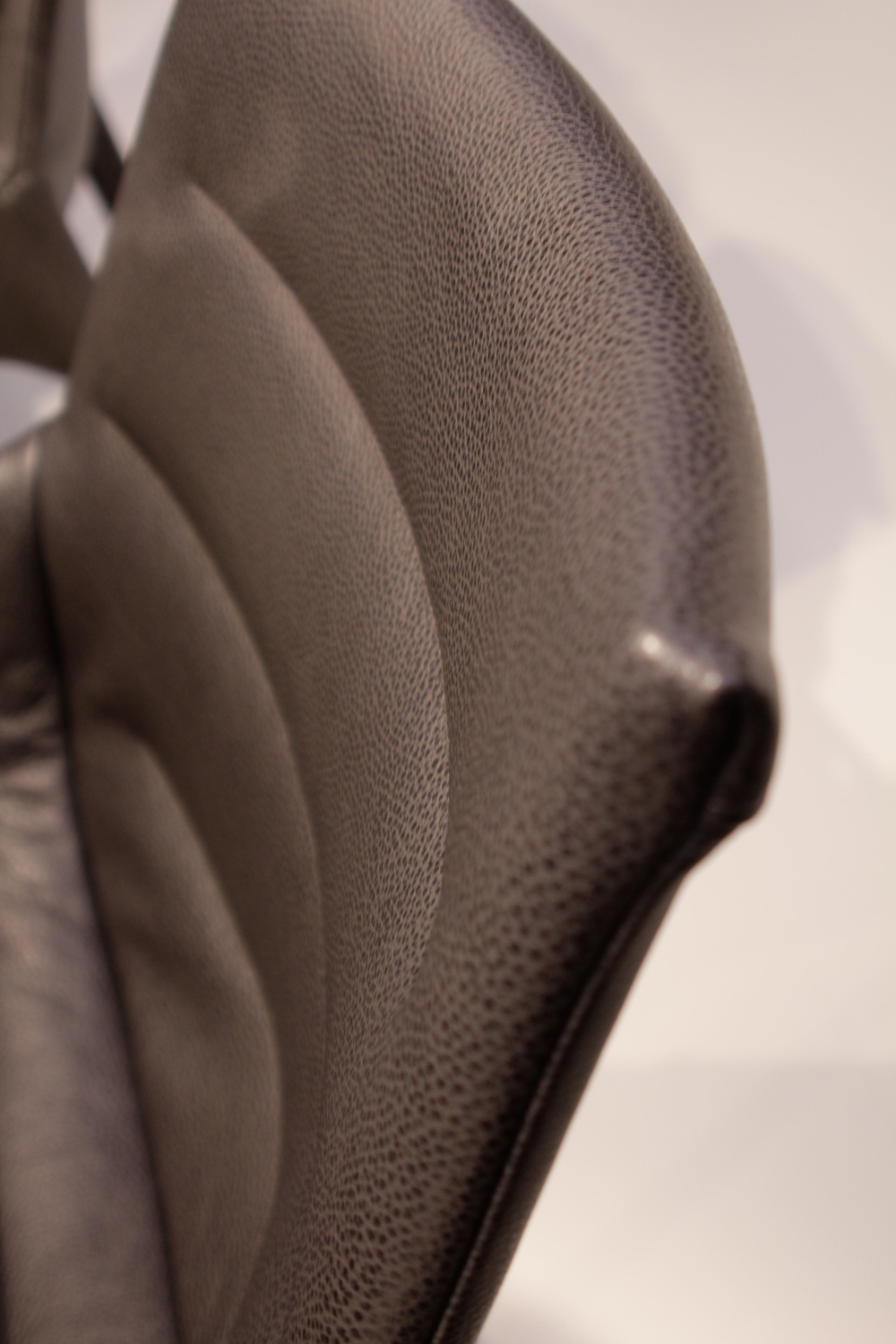
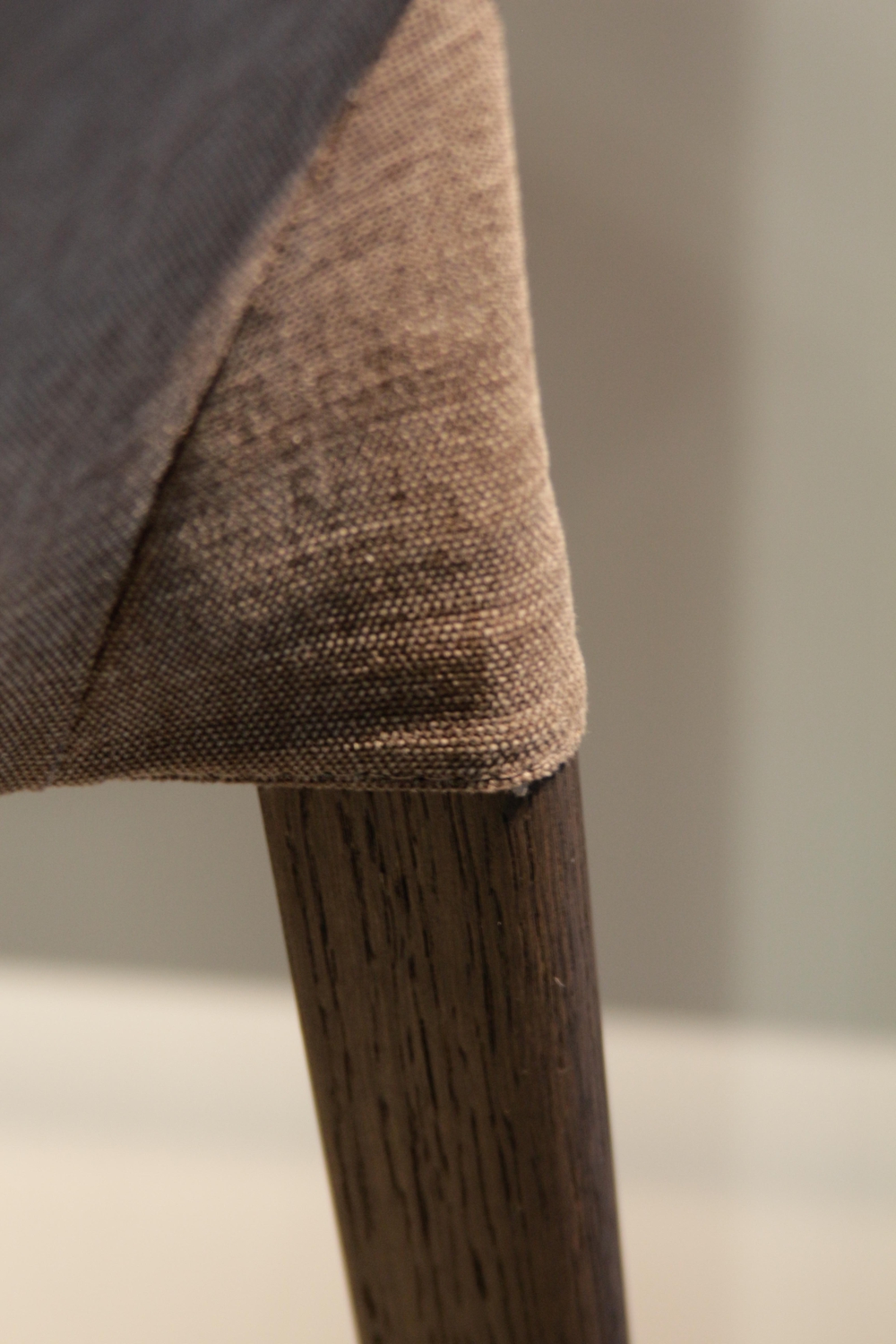
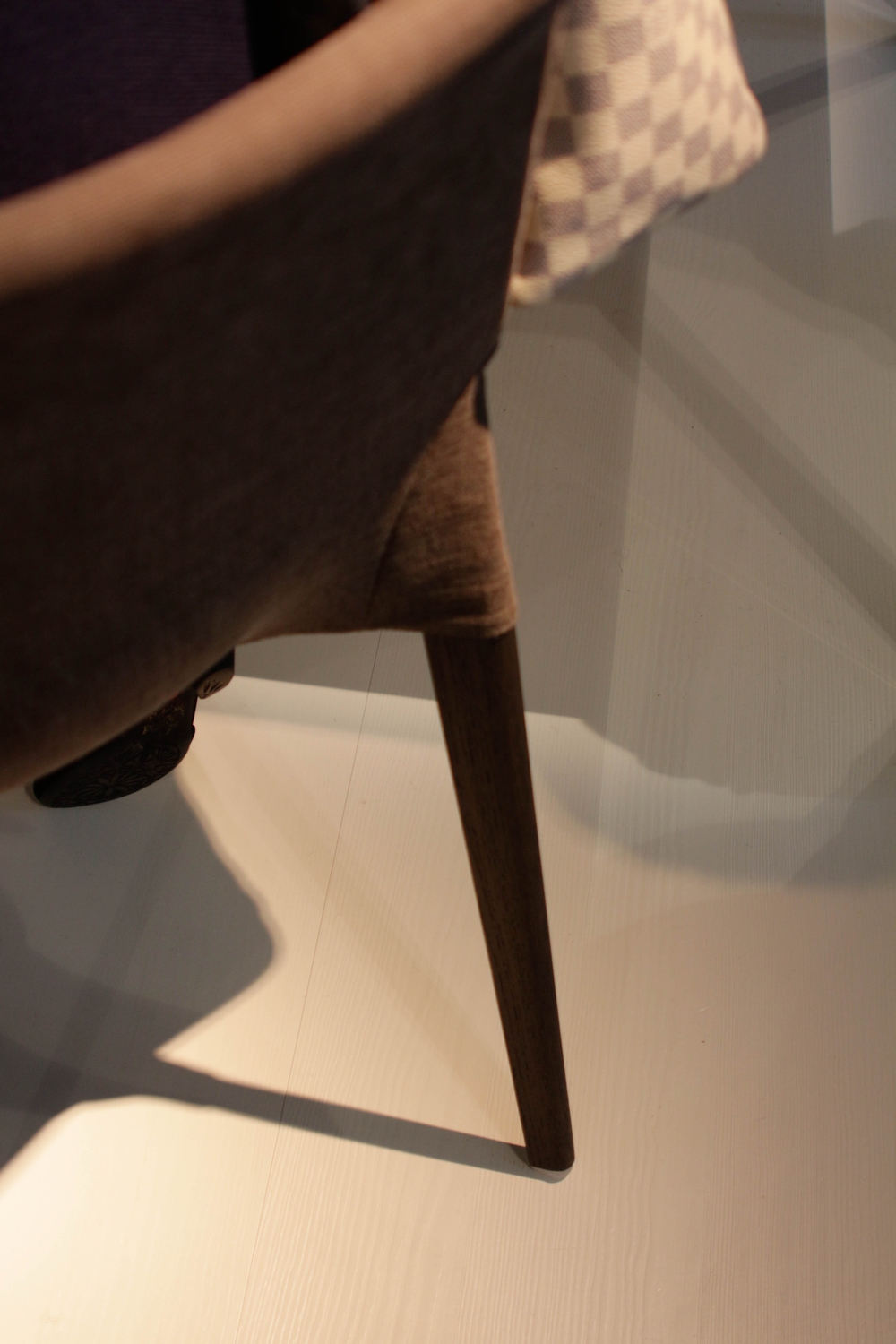
Need further information?
Register to download the full catalog, technical files andmuch more!

Back To Top